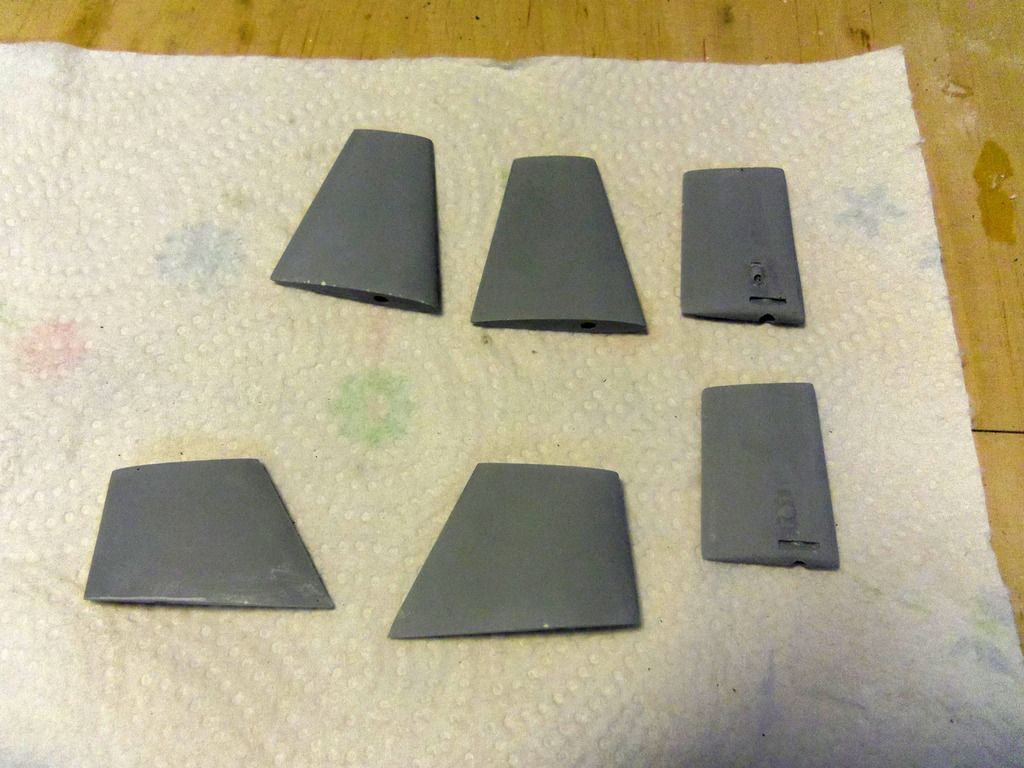
When everything is sanded, all surfaces are thoroughly cleaned of dust and then degreased using silicone remover.
The parts that mustn’t be painted are masked suing masking tape. Then all parts are fixed for the painting using auxiliary mounts.
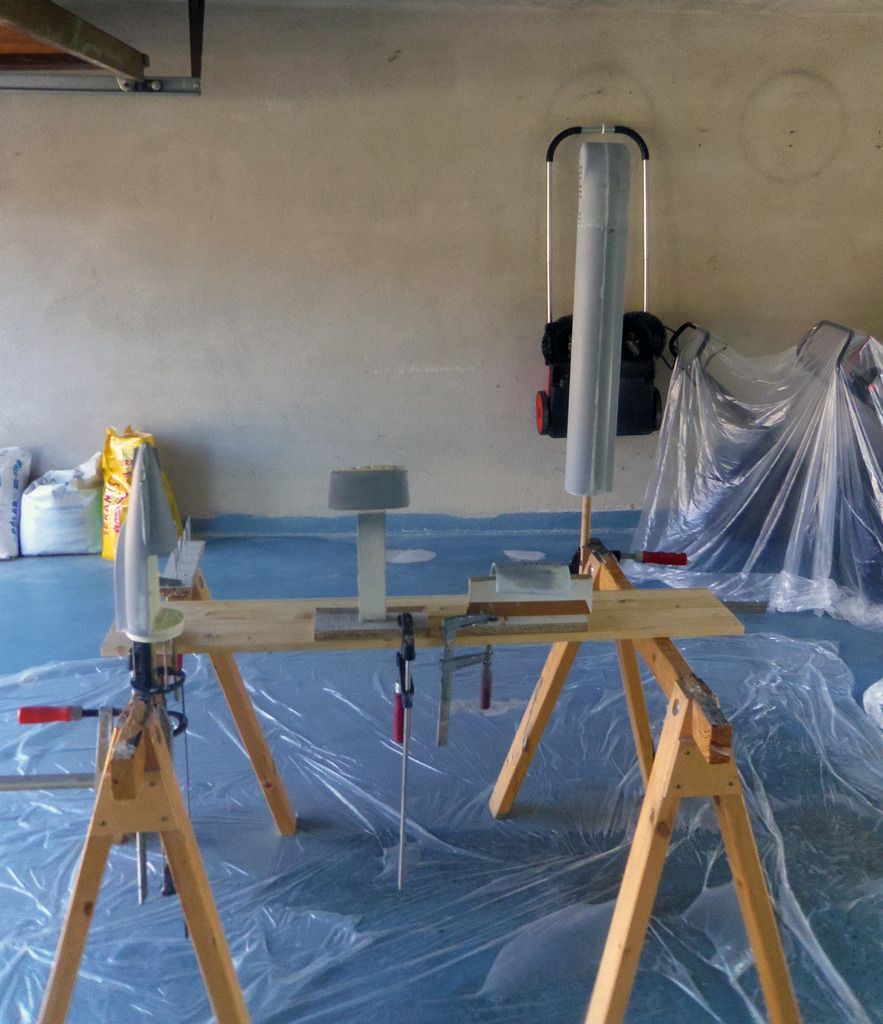
I use Südwest Allgrund 2-component filler/primer for the base coat, which I mix with 15% thinner (long). I apply the coat using a Satajet B (1,35 mm nozzle). It is important to thoroughly clean the room in which the paint is applied (here a garage) from dust and to clean all surfaces near the parts that are going to be painted using a wet cloth. The we are ready to go. Important: Use a breathing mask!!! Here the result:
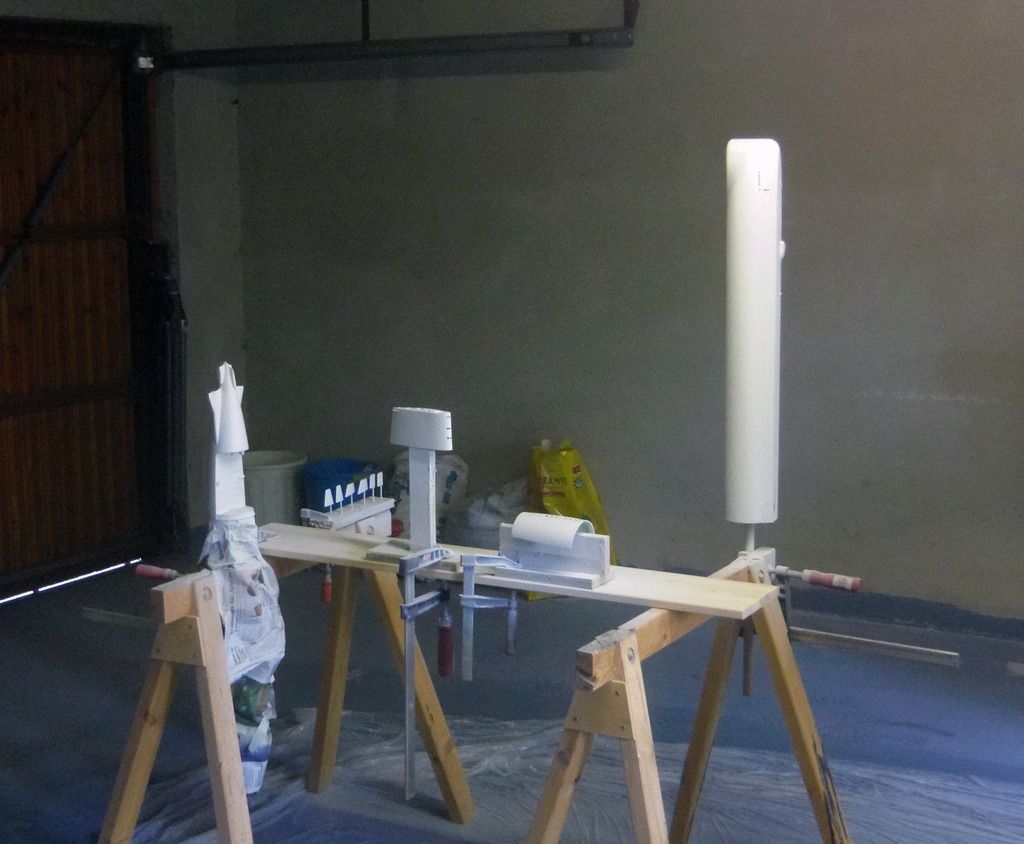
Now the remaining micro pores can be filled and then again everything is wet sanded using 600-grade sandpaper.
Leave a comment: