Fellow R/C submariners, here I am with my second project in the making.
I know, I know… why more than one project at the time? Do I really have to explain myself here?
In principle, the ALVIN is great but it is also quite unconventional and I was looking to gather some additional experience in parallel to that build by diving into a more conventional boat and use readily available cylinders.
I also value the lessons learned among both projects as they will inevitably influence each build in a positive fashion and in particular now that I have a lot to learn.
So, let’s get into it.
This is the 1:72 scale Collins Class from the Nautilus Drydocks files, it is a nice boat, stubby enough to push some water around and to offer plenty of room to make the build not too tight.
A nice size. Printing time is also reasonable, at a layer height of 0.2mm the overall time is approx. 8 days and 4 hours for a total of 1.8 kg of material. That is, printing at 100% infill all hull parts (including planes and other details), the additional components required to fit the cylinders and others will come on top of that time and material budget.
The files also comes with a decent stand, something that came in handy during the build.
By design, it is a Z-split hull but I saw videos where it was split differently (in particular the 1:54 version on Bob’s channel).
Here is the parts layout:
Senza titolo by Giacomo Bosso, su Flickr
Senza titolo by Giacomo Bosso, su Flickr
Please note I made the mistake of “shifting the sail” to the stern in the above picture… actually I pushed the mistake beyond the parts layout and glued the upper hull like this…
Ok, I had to print the five upper hull sections again, no way I could separate them afterwards. No problem, I will use them as weathering canvas to experiment with later on.
Anyway, the good thing about the design of this 3D printed parts is that you can slide 2.5mm diameter carbon rods into each section while glueing everything together.
This will make it very easy to keep everything aligned as you go.
Senza titolo by Giacomo Bosso, su Flickr
Senza titolo by Giacomo Bosso, su Flickr
I know, I know… why more than one project at the time? Do I really have to explain myself here?
In principle, the ALVIN is great but it is also quite unconventional and I was looking to gather some additional experience in parallel to that build by diving into a more conventional boat and use readily available cylinders.
I also value the lessons learned among both projects as they will inevitably influence each build in a positive fashion and in particular now that I have a lot to learn.
So, let’s get into it.
This is the 1:72 scale Collins Class from the Nautilus Drydocks files, it is a nice boat, stubby enough to push some water around and to offer plenty of room to make the build not too tight.
A nice size. Printing time is also reasonable, at a layer height of 0.2mm the overall time is approx. 8 days and 4 hours for a total of 1.8 kg of material. That is, printing at 100% infill all hull parts (including planes and other details), the additional components required to fit the cylinders and others will come on top of that time and material budget.
The files also comes with a decent stand, something that came in handy during the build.
By design, it is a Z-split hull but I saw videos where it was split differently (in particular the 1:54 version on Bob’s channel).
Here is the parts layout:

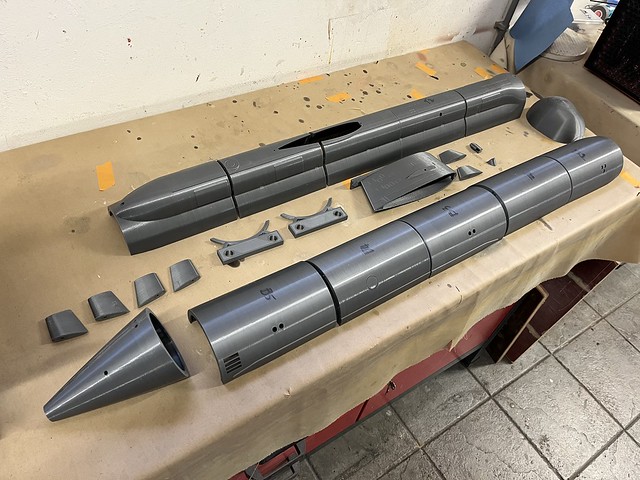
Please note I made the mistake of “shifting the sail” to the stern in the above picture… actually I pushed the mistake beyond the parts layout and glued the upper hull like this…
Ok, I had to print the five upper hull sections again, no way I could separate them afterwards. No problem, I will use them as weathering canvas to experiment with later on.
Anyway, the good thing about the design of this 3D printed parts is that you can slide 2.5mm diameter carbon rods into each section while glueing everything together.
This will make it very easy to keep everything aligned as you go.


Comment