Do you ever get to the point where in a large project, you kind of lose sight of what the final goal is and become a zombie and just go through the motions? That’s where I was at before I started in on the topic at hand, redoing the hull intermediate moulds over again.
The Seawolf has so many fine details, and I want to include as many as these as possible on my 1/72 replication of it. Included in this list is the bevelling effect produced where the thick anachoatic coating reaches a place where it can’t cover and hereby has to faired into the spot, hence the bevelling. This is such a visible detail that I feel it undeniably has to be on my boat in order to be faithful to the real thing. Also, the more detail the better. So here we go, now we’re going to be negative and make a positive thing from that...if you know what I mean
So, I guess we’ll start with the concept. I had to figure out how I was going to do this. I could make a solid hull plug, gouge away material and then somehow build bevels there; a concept that never really grabbed my interest in the slightest. All it would mean is a lot of work and I’m not guaranteed a great finished product. I could also build out from my already finished hull, but then that wouldn’t be scale. My last option, and the one I chose is by using some quick and dirty intermediate moulds so I could make negative detailing within them and then make two hull half master patterns from those.
My work so far with this has been on the sail first because it smaller and will give a good feel as to how things will work out when I get to the hull. The sail’s coating thickness and the hull’s are different, but the following description works for both. I started out by sticking some of my new best friend (two sided carpet tape) onto any scrap wood I had kicking around the shop, leaving the release paper still stuck to the back of the tape. I then stuck another layer of tape on top of the release paper and this time I remove the release paper from this second ply. From there I applied styrene of the appropriate thickness onto the tape. Both sides of the wood are run through the table saw to get perfect flush edges. With the saw I’m using a fine tooth melamine blade to ensure against any kind of plastic chipping that might come about.

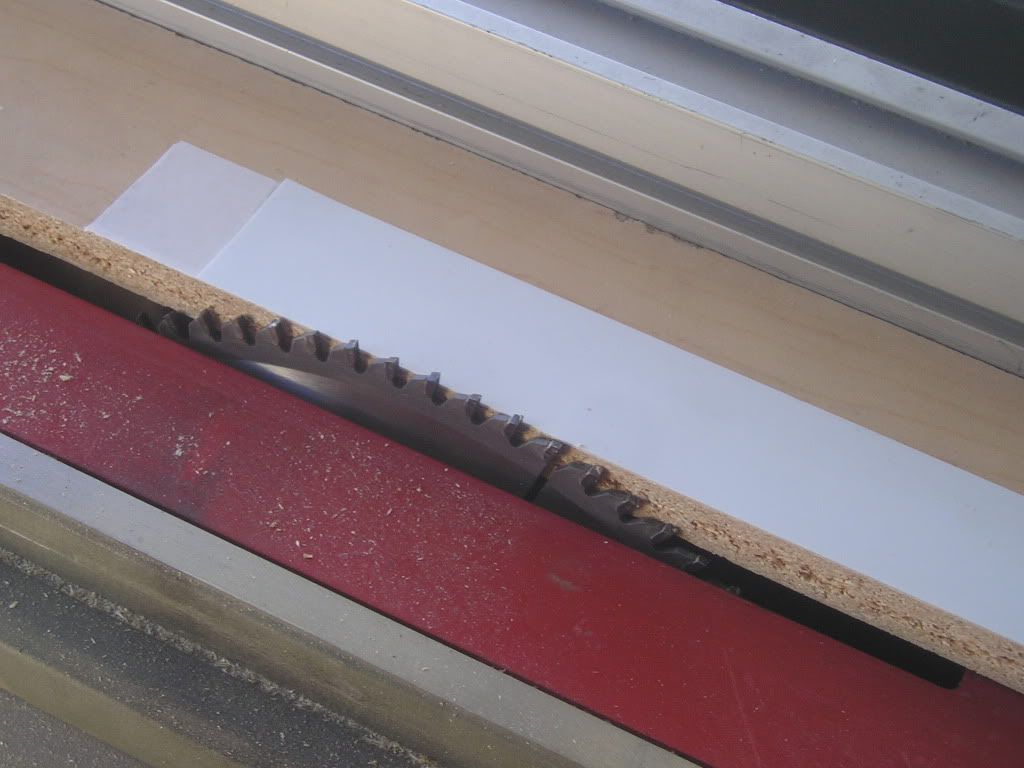
The laminated wood is taken over to my bench, where I clamped another wider piece of wood (this was run through the saw to ensure straightness) to my bench that was also around the same length as the laminated one. I then clamped the laminated board to this other board ensuring both top surfaces were perfectly flush with each other. This provided me with a flat surface in which I could run my little laminate trimmer (router) along and shape the styrene plastic. I do have a router table, but it would be too much of a pain in the rear to dig it out and set it up, so I settled on this other contraption which worked just fine anyway. Some notes here, the router bit with the angle I wanted was special, it was extremely hard to find in town here, and when I did find it, they wanted a special price for it! Also, I found that for better, cleaner results the bit had to be run backwards, meaning the router was pulled towards me, not pushed as per the norm.
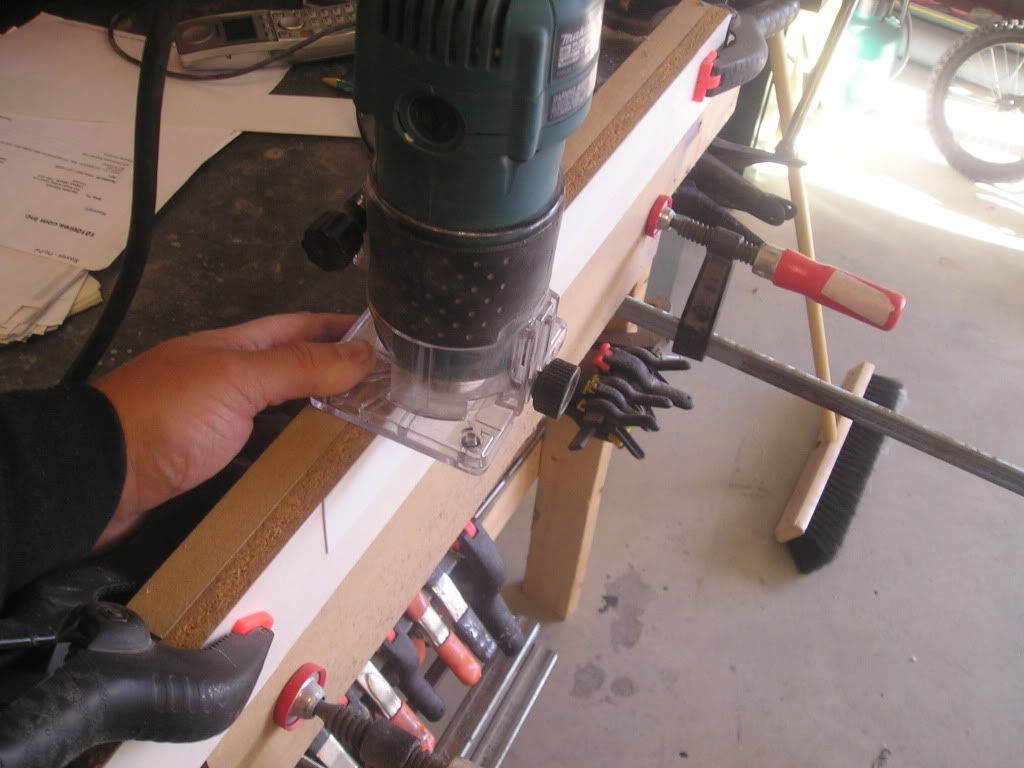
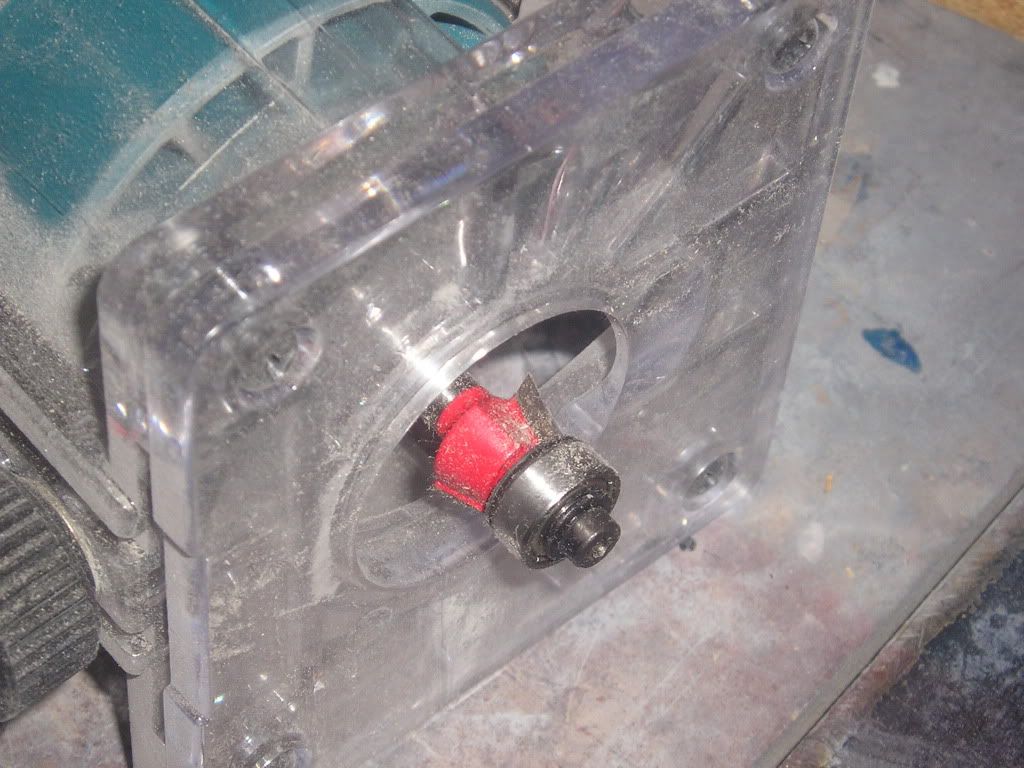
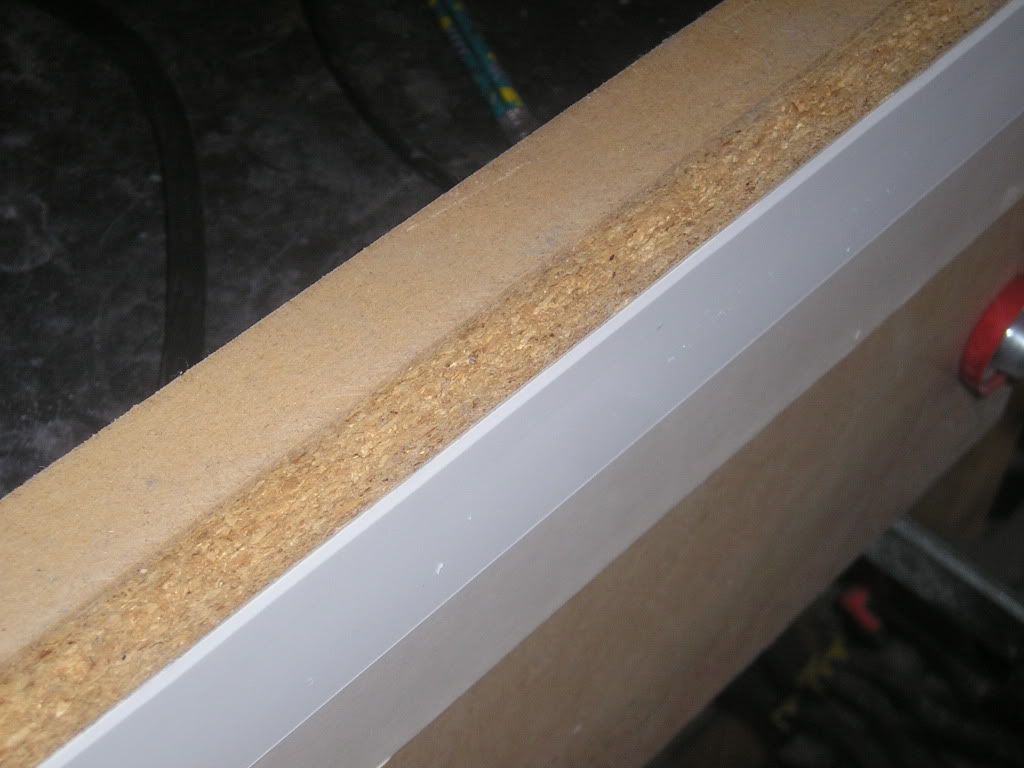
After each length was routed, I took the board back over to my saw and cut the bevelled plastic and its wood that it is stuck to, and then took the board back over to the router. This was repeated until I felt I had far more bevel strips than I needed, which probably means not enough! Also, the plastic remains stuck to the wood until which time that it is needed.
From here, it is now a matter of applying my plastic to wherever it is needed. The hard part for me on this is getting my mind to work in a mirror image, negative world to apply this stuff correctly. Sometimes I get confused and make things wrong he he. Simply peel the plastic off the separation paper on the board and then apply where needed. The carpet tape is more than adequate at holding down whatever needs to be secured. I love this stuff; I have big plans for the future for it! Bevelled corners are a matter of using a knife to cut the styrene, and even if they don’t match perfectly I just use a touch of red putty. This is nice for me because hardwood doesn’t have this kind of error factor when doing trim on houses or countertops.
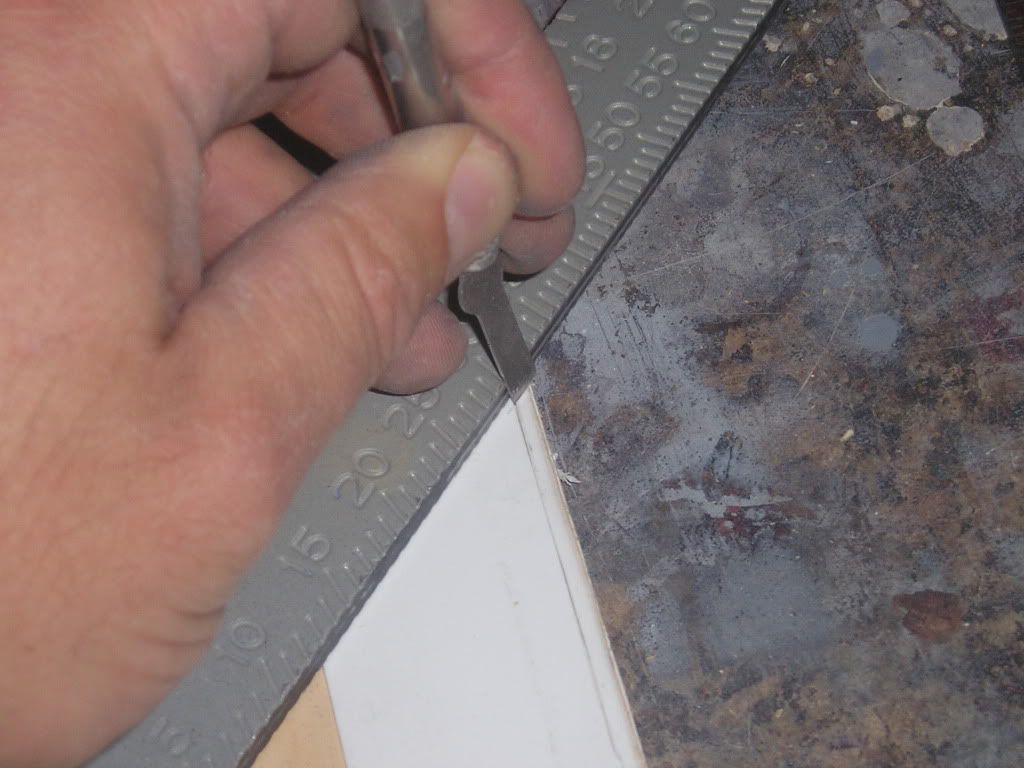
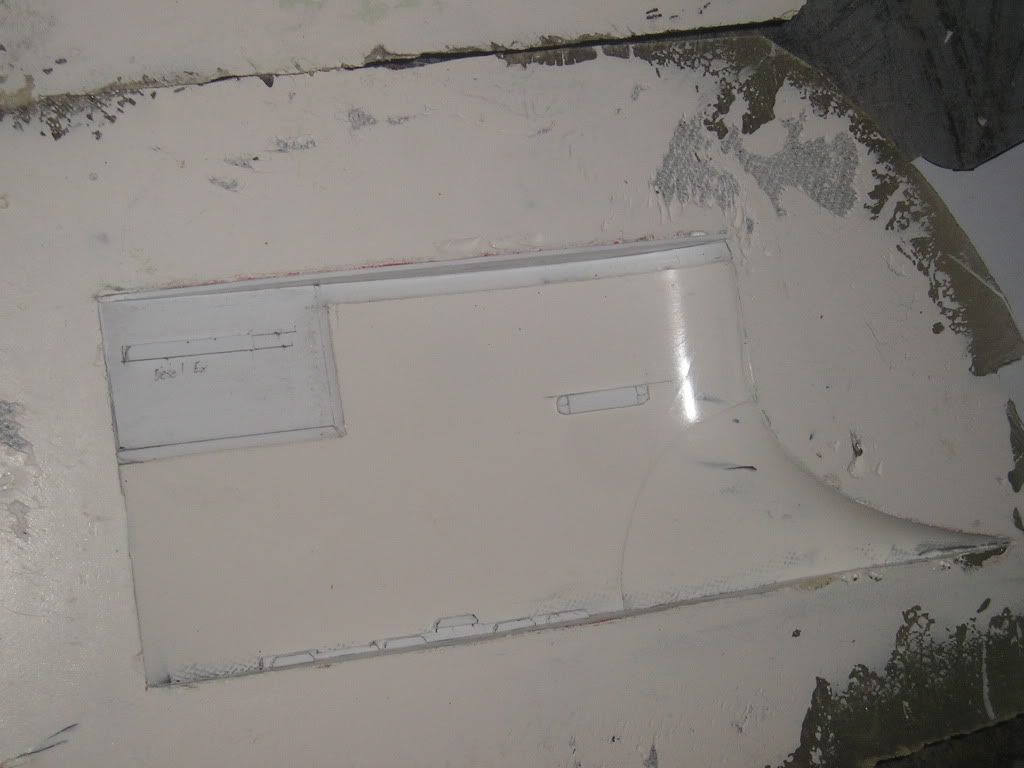
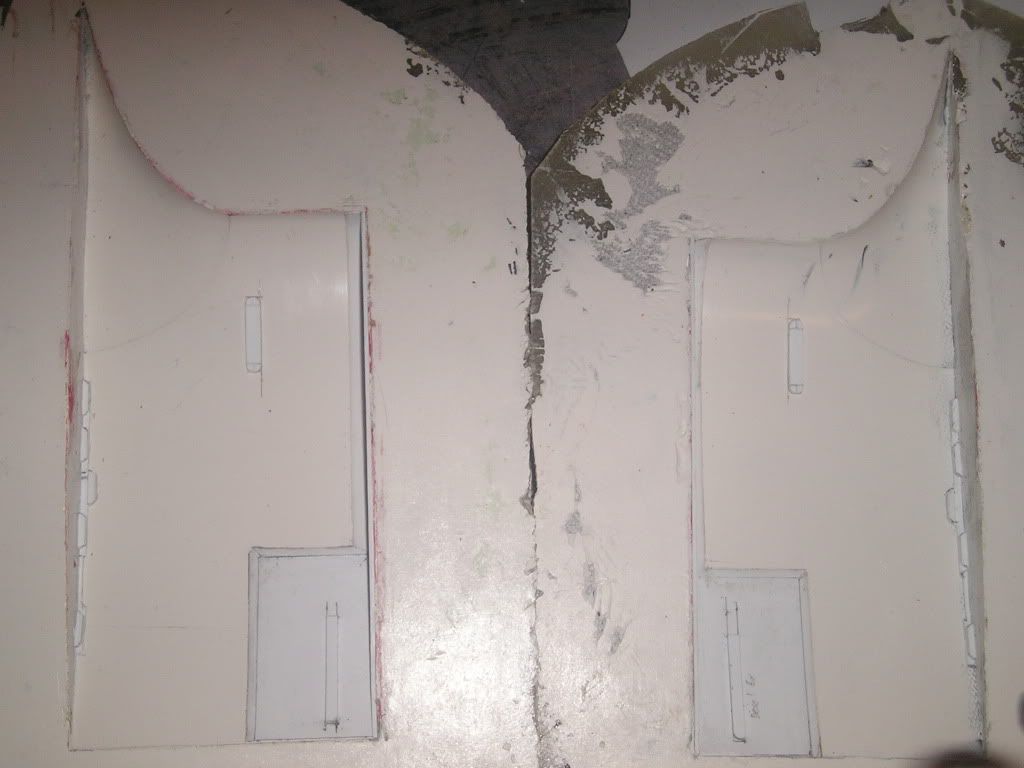
Now, this is cool. I can do more than just bevelling on these negatives, in the sail’s case I added drain holes at the bottom, and troughs in which the sidelights and diesel exhaust louvers can be put into the final master. This means there are some major possibilities and potential on the hull to take that even further than originally envisioned!
The Seawolf has so many fine details, and I want to include as many as these as possible on my 1/72 replication of it. Included in this list is the bevelling effect produced where the thick anachoatic coating reaches a place where it can’t cover and hereby has to faired into the spot, hence the bevelling. This is such a visible detail that I feel it undeniably has to be on my boat in order to be faithful to the real thing. Also, the more detail the better. So here we go, now we’re going to be negative and make a positive thing from that...if you know what I mean
So, I guess we’ll start with the concept. I had to figure out how I was going to do this. I could make a solid hull plug, gouge away material and then somehow build bevels there; a concept that never really grabbed my interest in the slightest. All it would mean is a lot of work and I’m not guaranteed a great finished product. I could also build out from my already finished hull, but then that wouldn’t be scale. My last option, and the one I chose is by using some quick and dirty intermediate moulds so I could make negative detailing within them and then make two hull half master patterns from those.
My work so far with this has been on the sail first because it smaller and will give a good feel as to how things will work out when I get to the hull. The sail’s coating thickness and the hull’s are different, but the following description works for both. I started out by sticking some of my new best friend (two sided carpet tape) onto any scrap wood I had kicking around the shop, leaving the release paper still stuck to the back of the tape. I then stuck another layer of tape on top of the release paper and this time I remove the release paper from this second ply. From there I applied styrene of the appropriate thickness onto the tape. Both sides of the wood are run through the table saw to get perfect flush edges. With the saw I’m using a fine tooth melamine blade to ensure against any kind of plastic chipping that might come about.

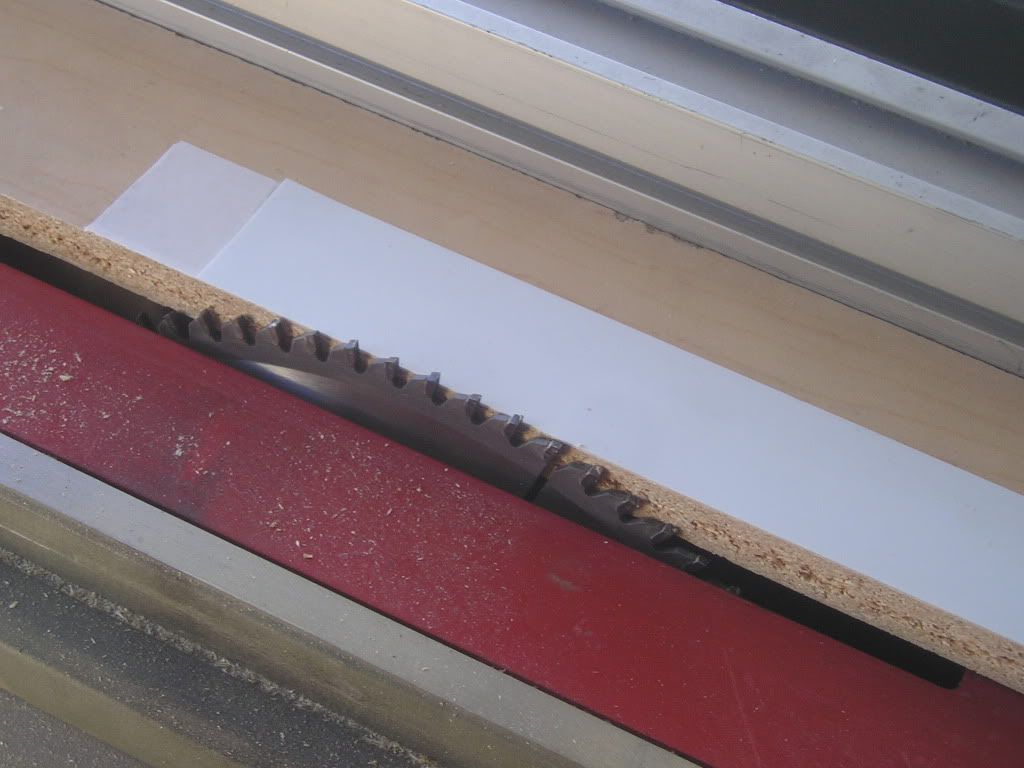
The laminated wood is taken over to my bench, where I clamped another wider piece of wood (this was run through the saw to ensure straightness) to my bench that was also around the same length as the laminated one. I then clamped the laminated board to this other board ensuring both top surfaces were perfectly flush with each other. This provided me with a flat surface in which I could run my little laminate trimmer (router) along and shape the styrene plastic. I do have a router table, but it would be too much of a pain in the rear to dig it out and set it up, so I settled on this other contraption which worked just fine anyway. Some notes here, the router bit with the angle I wanted was special, it was extremely hard to find in town here, and when I did find it, they wanted a special price for it! Also, I found that for better, cleaner results the bit had to be run backwards, meaning the router was pulled towards me, not pushed as per the norm.
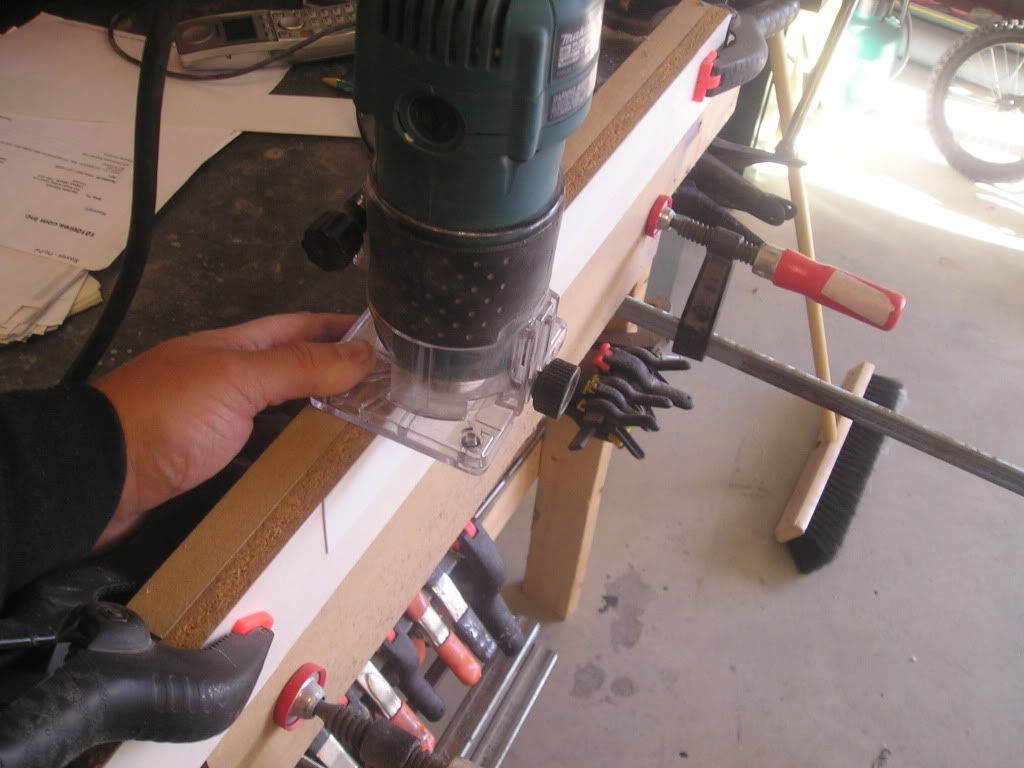
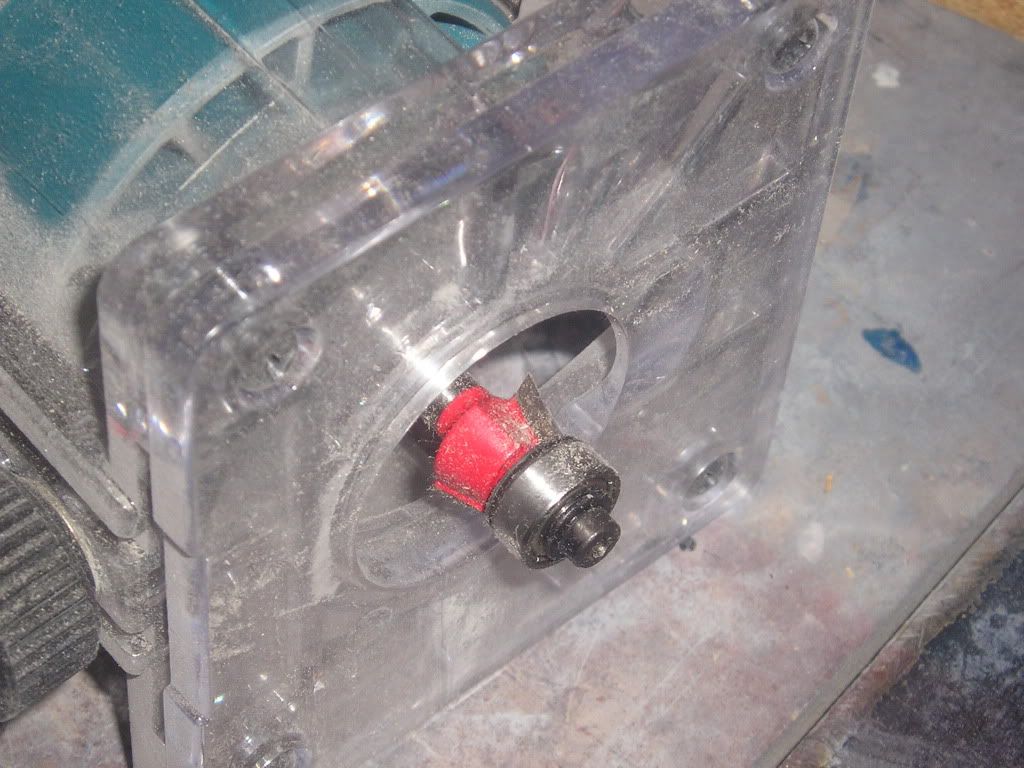
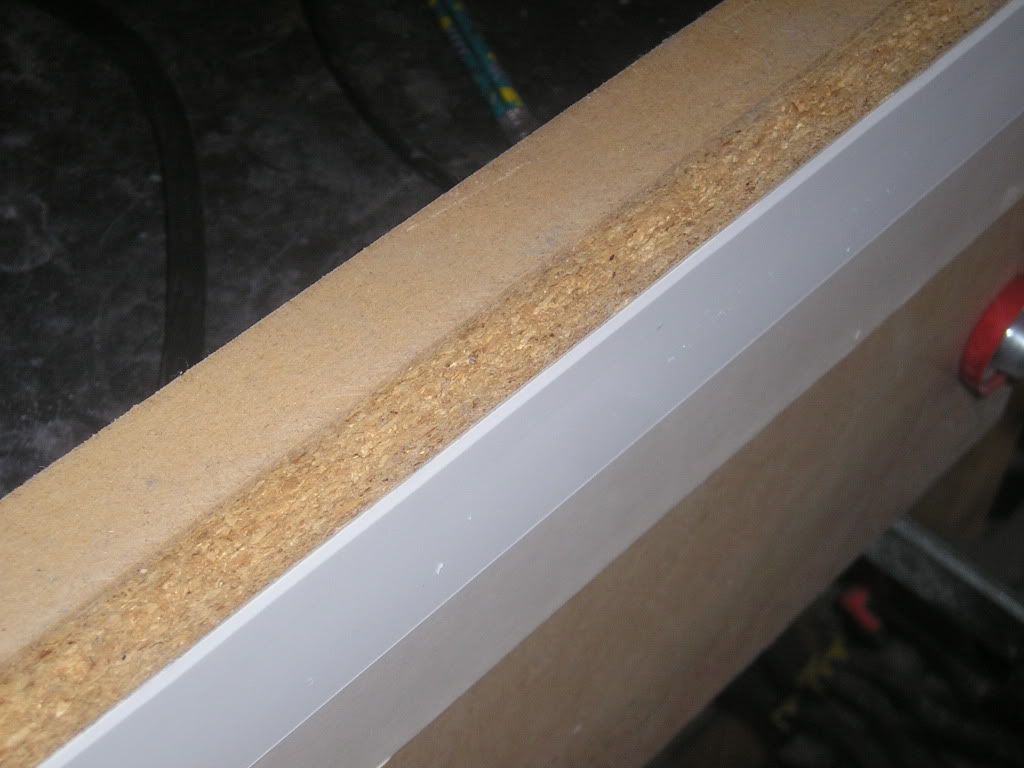
After each length was routed, I took the board back over to my saw and cut the bevelled plastic and its wood that it is stuck to, and then took the board back over to the router. This was repeated until I felt I had far more bevel strips than I needed, which probably means not enough! Also, the plastic remains stuck to the wood until which time that it is needed.
From here, it is now a matter of applying my plastic to wherever it is needed. The hard part for me on this is getting my mind to work in a mirror image, negative world to apply this stuff correctly. Sometimes I get confused and make things wrong he he. Simply peel the plastic off the separation paper on the board and then apply where needed. The carpet tape is more than adequate at holding down whatever needs to be secured. I love this stuff; I have big plans for the future for it! Bevelled corners are a matter of using a knife to cut the styrene, and even if they don’t match perfectly I just use a touch of red putty. This is nice for me because hardwood doesn’t have this kind of error factor when doing trim on houses or countertops.
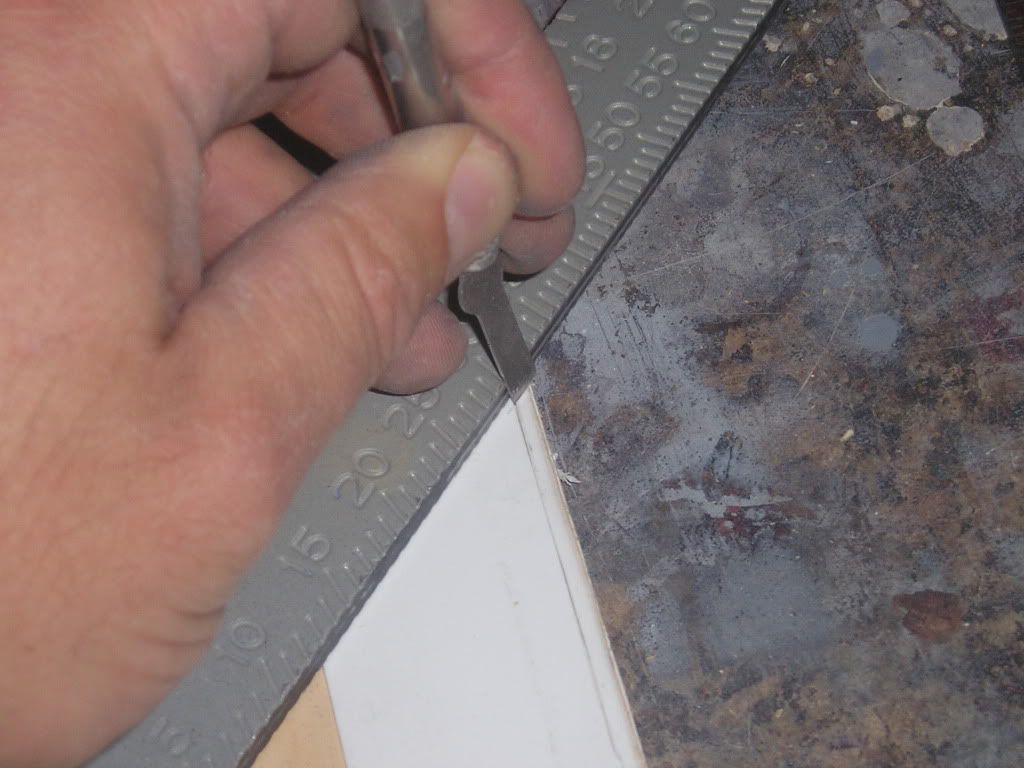
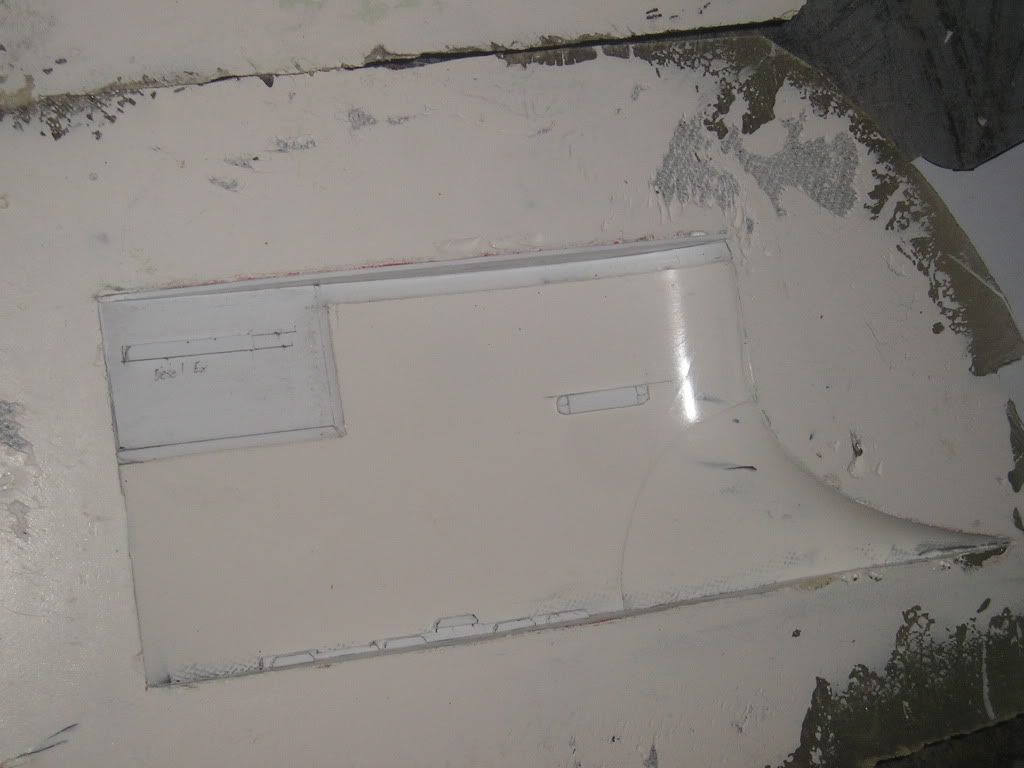
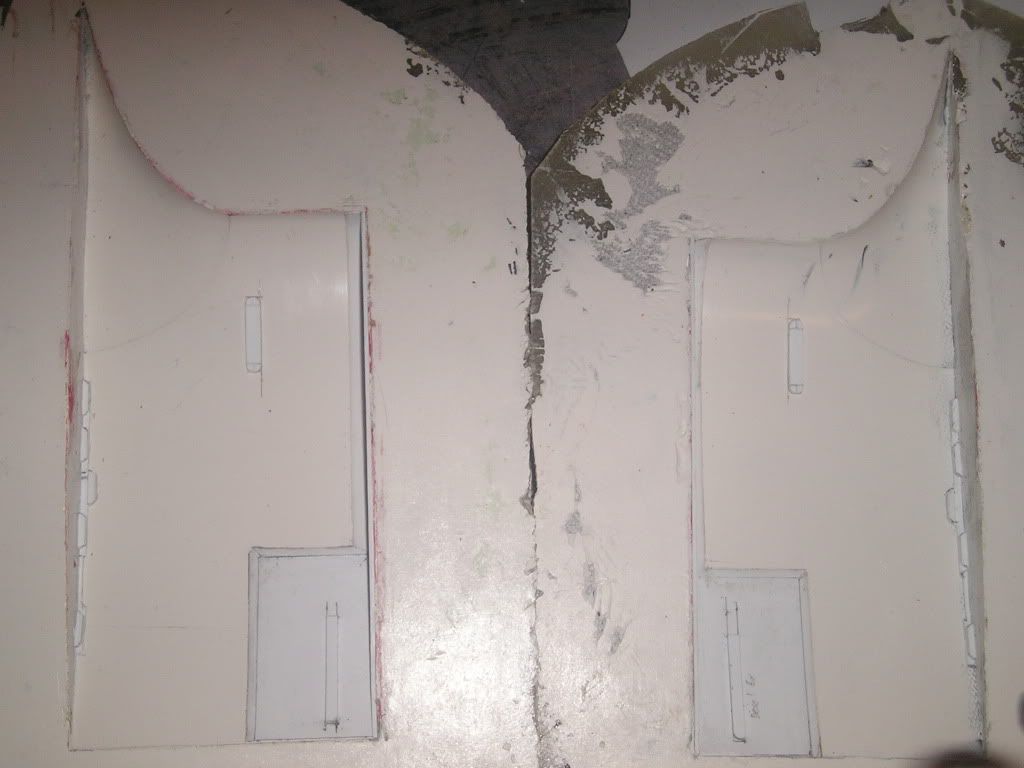
Now, this is cool. I can do more than just bevelling on these negatives, in the sail’s case I added drain holes at the bottom, and troughs in which the sidelights and diesel exhaust louvers can be put into the final master. This means there are some major possibilities and potential on the hull to take that even further than originally envisioned!
Comment