First, that angled induction tube is inviting a hang-up of the vertically sliding float with attached rubber element.
Second, that very very large intake that mates with the face of the rubber element presents so much surface area that even the slightest of differential pressures between atmosphere and the interior of the cylinder will keep the float valve in the 'closed' condition even when the float rises above the water -- the vacuum will keep it closed.
differential force is a function of intake opening area -- the smaller the opening the less force the differential exerts to keep the valve closed.
Third, the center of floatation is so far removed from where the float slides on the induction tube that it invites the slide bushing within the float to kink and jam on the vertical portion of the induction tube.
Third, the center of floatation is so far removed from where the float slides on the induction tube that it invites the slide bushing within the float to kink and jam on the vertical portion of the induction tube.
Re-make the snorkel assembly to look like mine. And make the snorkel intake opening .030" diameter.
This is a properly designed snorkel head-valve assembly:
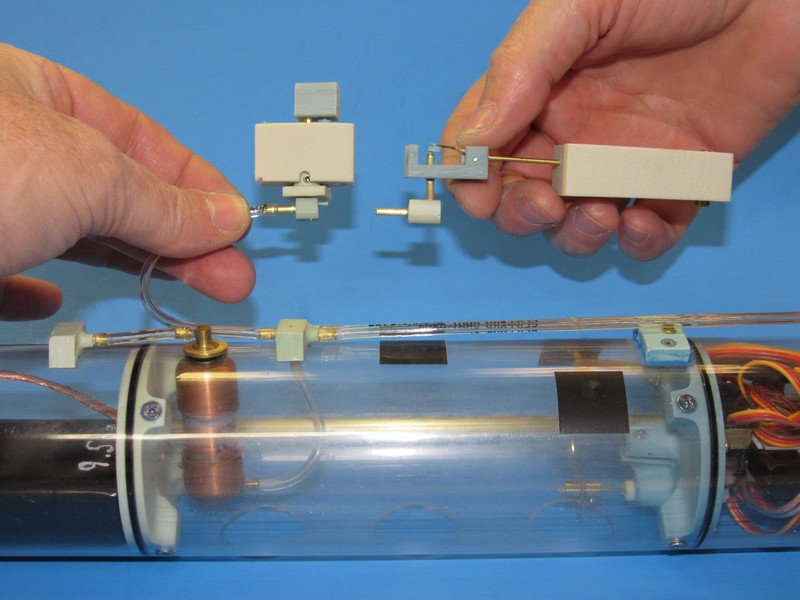
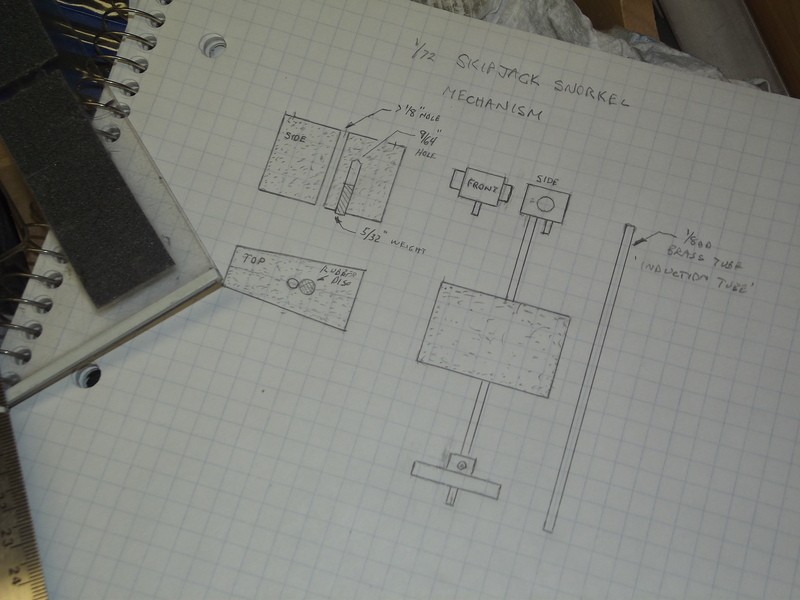
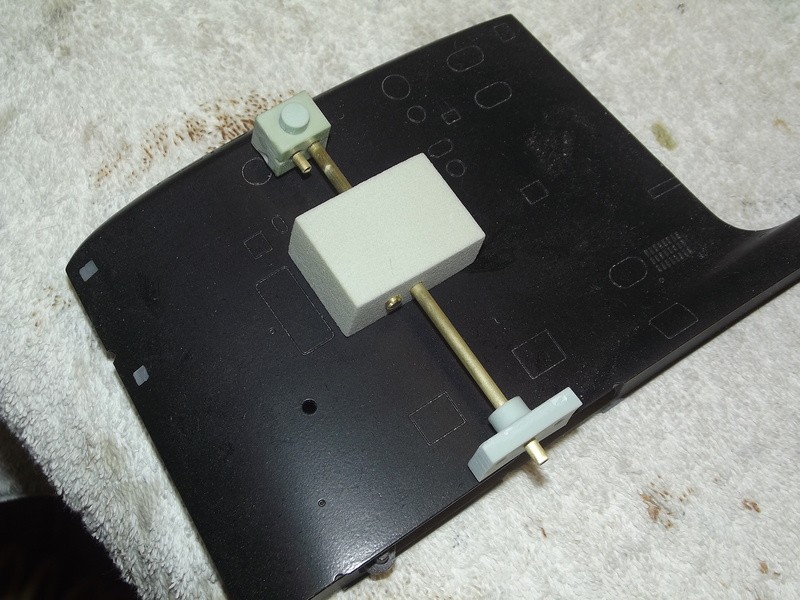

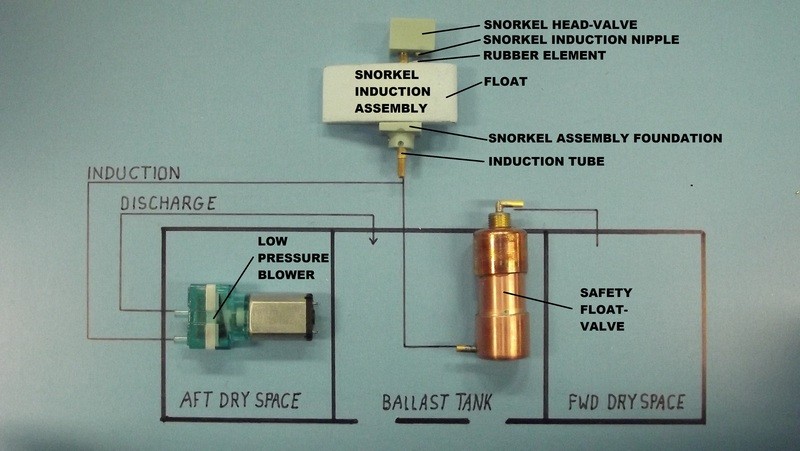
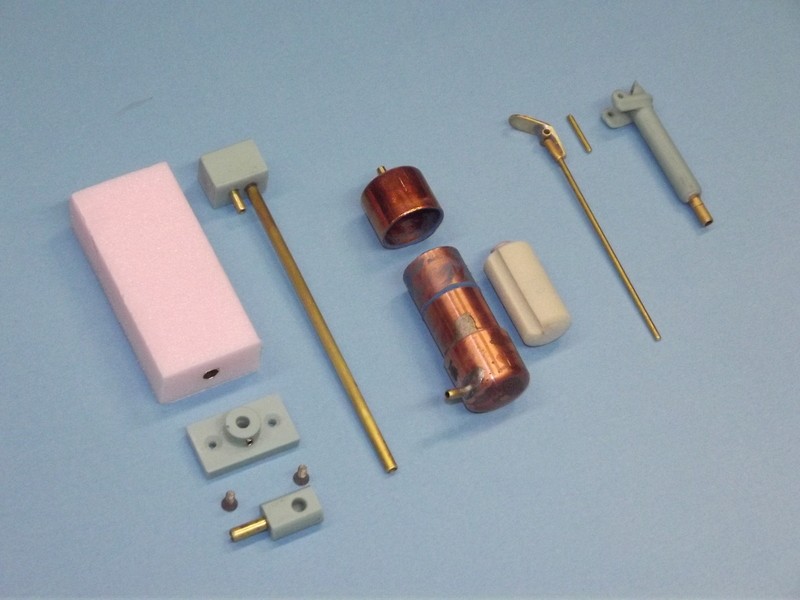
David
Leave a comment: